Welding WPS: Common Errors to Stay Clear Of and How to Correct Them
Welding WPS: Common Errors to Stay Clear Of and How to Correct Them
Blog Article
Opening the Power of Welding WPS: Methods for Effectiveness and Safety in Manufacture
In the world of manufacture, Welding Procedure Specifications (WPS) stand as the foundation of welding procedures, determining the essential steps for attaining both performance and security in the fabrication process. Recognizing the details of WPS is critical to harnessing its full potential, yet many companies have a hard time to unlock truth power that exists within these papers (welding WPS). By diving right into the approaches that enhance welding WPS, a world of boosted productivity and enhanced security waits for those eager to discover the nuances of this important facet of construction

Significance of Welding WPS
The value of Welding Procedure Specifications (WPS) in the fabrication sector can not be overstated. WPS work as an important roadmap that lays out the needed actions to make certain welds are executed regularly and correctly. By specifying important criteria such as welding procedures, products, joint layouts, preheat temperatures, interpass temperatures, filler metals, and post-weld heat treatment demands, WPS give a standardized approach to welding that boosts effectiveness, high quality, and safety and security in manufacture processes.
Adherence to WPS aids in attaining uniformity in weld high quality, reducing the likelihood of flaws or architectural failings. This standardization additionally assists in compliance with sector regulations and codes, making certain that produced structures meet the called for security criteria. Moreover, WPS paperwork allows welders to duplicate successful welding treatments, resulting in consistent outcomes across different tasks.
Essentially, the careful development and stringent adherence to Welding Procedure Specs are extremely important for promoting the honesty of welded frameworks, safeguarding against potential risks, and promoting the credibility of manufacture firms for delivering top notch services and products.
Crucial Element of Welding WPS
Enhancing Effectiveness With WPS
When optimizing welding procedures, leveraging the crucial elements laid out in Welding Treatment Specifications (WPS) becomes crucial for making the most of and streamlining procedures productivity. One means to improve effectiveness with WPS is by thoroughly selecting the suitable welding specifications. By sticking to the particular standards provided in the WPS, welders can make sure that the welding devices is established correctly, bring about high-quality and consistent welds. Additionally, adhering to the pre-approved welding sequences outlined in the WPS can substantially lower the moment spent on each weld, ultimately boosting overall performance.
Additionally, appropriate training and certification of welders in understanding and implementing WPS can even more improve performance. Ensuring that all staff member are skilled in analyzing and executing the WPS precisely can lessen mistakes and revamp, conserving both time and resources. Frequently assessing and updating the WPS to include any lessons learned or technical improvements can also add to performance enhancements in welding operations. By embracing the guidelines stated in the WPS and continually seeking ways to maximize procedures, fabricators can attain greater effectiveness degrees and exceptional end outcomes.
Ensuring Security in Construction
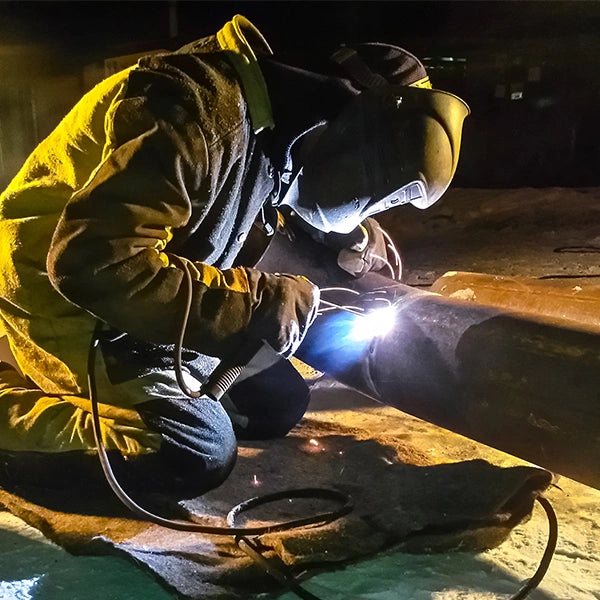
Making sure safety in construction entails a multifaceted technique that includes various aspects of the welding process. Welders have to be outfitted with appropriate equipment such as helmets, handwear covers, and protective clothing to minimize dangers connected with welding tasks.
Furthermore, adherence to correct air flow and fume extraction systems is crucial in keeping a healthy workplace. Welding fumes consist of damaging compounds that, if breathed in, can position severe health risks. weblink Implementing reliable air flow procedures Get More Information aids to minimize exposure to these unsafe fumes, advertising respiratory health and wellness amongst employees.
Routine tools maintenance and inspections are additionally necessary for making sure safety and security in construction. Defective machinery can result in injuries and crashes, underscoring the value of prompt repair work and regular checks. By prioritizing safety and security measures and fostering a society of understanding, manufacture facilities can create a secure and productive work atmosphere for their personnel.
Applying WPS Best Practices
To boost operational efficiency and guarantee top quality results in fabrication processes, integrating Welding Treatment Specification (WPS) ideal methods is paramount. Picking the proper welding procedure, filler product, and preheat temperature level specified in the WPS is critical for achieving the preferred weld top quality. Guaranteeing that certified welders with the essential accreditations lug out the welding treatments according to the WPS standards is crucial for uniformity and integrity.
Final Thought
In verdict, welding WPS plays a vital function in ensuring performance and security in fabrication processes. By concentrating on crucial elements, enhancing efficiency, and carrying out best methods, firms can enhance their welding operations. It is important to focus on precaution to avoid crashes and ensure a smooth manufacturing process. By complying with these strategies, organizations can unlock the full potential of welding WPS in their construction operations.
In the world of construction, his comment is here Welding Procedure Specs (WPS) stand as the backbone of welding operations, determining the necessary actions for accomplishing both performance and security in the fabrication procedure. By defining essential criteria such as welding processes, products, joint designs, preheat temperatures, interpass temperature levels, filler metals, and post-weld warm treatment demands, WPS offer a standard technique to welding that enhances efficiency, high quality, and security in fabrication procedures.

When optimizing welding procedures, leveraging the crucial aspects detailed in Welding Treatment Specs (WPS) becomes crucial for making best use of and streamlining processes efficiency. (welding WPS)
Report this page